But first, check out all the places we are delivering training this month...
Why do many safety change initiatives fail to achieve expected results?
Inevitably organizations face the need for some form of change in order to garner improvement in operational results, performance of their employees, financial outcomes, etc. This then leads to an analysis of the situation, a selection of an intervention, which is then deployed in order to solve the problem or gain an improvement in results. It is a proven fact that much of the deployed change initiative fails to deliver the expected improvements. There are many reasons for the degree of this failure as indicated by the following researched data:
- Up to 70% of all change initiatives fail to achieve expected improvement.
- Virtually all change initiatives have inherent problems.
- Almost 90% of companies trained their managers in managing change but about 20% felt the training was effective.
- Almost 70% of senior managers said they understood the need for change, this dropped to 50% for managers, and 40% for supervisors.
- About 50% of employees felt the deployed change initiatives met the initial objective, but only 20% felt gains were sustained over time.
- 30% of change initiatives fail due to faulty deployment practices
Improvement initiatives in safety face even a greater challenge to overcome due to some structural issues inherent in the administration of core operational processes, management procedures, and safety practices. This is manifested in:
- The project supervision is responsible for planning, directing, and controlling production as well as quality while the safety manager is responsible for just worker safety.
- Most of the construction hazards are created by the natural progression of the work as it is put in place, while safety is responsible to find and correct them.
- The schedule drives production while safety is managed by inspections and loss data.
- The focus of operations is mostly proactive while safety in primarily reactive.
Traditional safety management
The underlying reason for the organization’s safety outcomes is the focus on changing the individual employee’s work behavior without implementing any changes to the organizational or operational systems or practices which ultimately drive their accidents and losses. Some improvement occurs after change implementation but eventually things seem to revert back to past outcomes. All one has to do is study the “Hawthorne Effect” to understand this.
Minor operational discrepancies or failures in construction are generally tolerated and change initiative are only undertaken when the negative results are not tolerable any longer. The methods used by management to change the unacceptable situation may include the traditional intervention, driven by the belief that the worker has virtual control over the situation in which they find themselves. To paraphrase the domino theory the immediate act prior to the adverse outcome’s occurrence is performed by the worker. So, the logical conclusion is that if this person had done things differently the outcome would have been different (acceptable); resulting in the application of the traditional safety interventions in order to eliminate the unacceptable outcomes.
To improve results, some may try to copy what another organization is doing, they may hire a new safety manager in the hopes that this person will somehow improve their safety outcome, or senior management may announce a new bold initiative intended to bring about dramatic performance improvement. In all probability these efforts will fail due to the fact that the organization is not addressing the underlying causes of the problem or they do not deploy the change initiative properly.
This obviously requires a well devised and robust change initiative to be devised and implemented. Change initiatives invariably have downsides. Employees generally do not like any form of change. Change may cause stress or some form of “pain” through uncertainty, lack of clear information, disruption of the work routine, misunderstanding of the potential impact on the work, etc. A significant amount of the unnecessary disruption, distress, or distraction can be avoided. Some of the possible factors impeding the successful implementation of change include:
- Failing to articulate a compelling vision or devising an integrated strategy
- Failing to create a powerful guiding coalition and remove barriers to excellence
- Allowing the normalization of deviations and employee complacency
- Failing to implement systems to sustain the change, supported by short term achievable wins
- Failing to properly empower and enable employees
- Failing to change the work climate and culture
- Elimination of dysfunctional behaviors
- Claiming victory too soon
As mentioned above one of the typical safety change initiative rollouts usually occurs after the annual review of the organization’s accident and loss picture. One of the long-term down sides of engaging in such a repetitive change implementation process is that any change initiative is views with skepticism, and employees view them as “flavor of the month”. The change initiative is not taken seriously, and management loses credibility, this almost guarantees the next initiative’s failure. To ensure the success of the change initiatives, organizational systems, processes, practices and procedures must be integrated and aligned, so as to enhance the acceptance of the change initiative by the employees as well as enable the successful implementation of the change process prior to the launching of the initiative.
Change initiative process elements
To implement change successfully the organization must have a robust well-defined process in place prior to the launching of a change initiative. This process has six elements. These elements take task related, emotional, behavioral, as well as metrics factors into consideration.
These elements are briefly described below:
Examine — What is wrong (present state). How things should be working (the Ideal state). The collection of relevant data in order to understand what is wrong and the analysis of the data to find the appropriate means of improving the conditions or the situation.
Consider — To ensure that the change initiative is accepted by the employees, management must articulate the underlying vision, so the employees understand the need for it. They must build excitement for it by explaining the benefit to the organization as well as to the workforce which will result from the changes. They must create teams to provide input and define the process by which to accomplish the change. Devise a robust strategy for implementation, Define the scope of the initiative, Set objectives with target milestones for the implementation.
Devise — Assign a champion to closely oversee the change process. Mobilize all the employee in the deployment and work toward acceptance of the changes, Test the strategy to ensure it is “right” for the situation. Energize everyone, Coach those that need assistance and mentor those who may need some encouragement. Refine anything that is not quite in line with the overriding premise.
Implement — Roll out the change initiative, involve everyone. Closely monitor the process as well as the reaction of the people. Ensure that everything is in line with goals, objectives as well as expectations. Identify barriers and solicit input to expeditiously find solution to problems or barriers.
Monitor — Collect data in order to determine if things are progressing in line with the goals, objectives as well as expectations resulting from the change. Solicit input. Evaluate the data and present results to management, inform everyone, of the progress and intermittent goal achievement. Identify areas that may need adjustment. Assess progress toward goal achievement.
Accept, Improve, or Modify — Realign elements of the process that requires improvement. Ensure the effectiveness of the change initiative implementation toward complete success.
Steps to sustain change improvements
To ensure that the change initiative not only is implemented successfully and is accepted by the employees but that the expected improvement is sustained over time, requires the changes to be institutionalized in the organization.
Firstly, the organizational systems must be checked to determine if there are misalignments in their interaction with each other which may drive or contribute to the conditions which created the discrepancies encountered. Management must ensure that the systems are integrated in such a way that they function in complete harmony with each other. The systems must operate in such a way so as to enable to workers to perform their work efficiently, effectively as well as safely.
The next area that needs to be addressed is the people factors to determine if these in some way have generated the unacceptable discrepancies. The people must be encouraged to be fully involved in the procedures and practices in order to perform their tasks well. Management must discourage deviations in procedures and practices.
Management must create a work climate which is conducive for workers to identify barriers to performance and voice suggested changes. Managers must actively oversee the basic function of management to ensure that deviations are not allowed to creep into procedures and practices thereby leading to the creation of discrepancies.
Conclusions
To create enabling conditions so as to ensure the implementation of change as well as sustaining the improvement garnered from the change two areas need to be addressed. These are the system factors as well as the people factors. Involve the people in identifying the good points and the not so good point of the policies, procedures, and practices. Create teams of people to work on coming up with better ways of doing what is not working well, or even with new way of doing things. This will in all likelihood diminish or even eliminate resistance and uncertainty associated with the change.
Source: ISHN Oct 2023
Company that closed after fatal accident fined $100K
In a tragic incident that underscores the critical importance of workplace safety measures, GTA Granite and Marble Countertops Inc. was fined $100,000 following a fatal accident that preceded the closure of the company.
The Ontario Court of Justice in Toronto imposed the fine after the company pled guilty to charges related to the accident. The court also applied a 25 percent victim fine surcharge, as mandated by the Provincial Offences Act, with the proceeds earmarked to support crime victims.
The accident happened on October 8, 2021, at the company's workplace in Toronto. A worker was crushed by a massive slab of granite that tipped over during its removal from a storage rack.
The Ministry of Labour, Immigration, Training and Skills Development found the company had failed to ensure the safe removal of the stone slab.
The task at hand involved retrieving a 1,100-pound granite slab stored on a wooden A-frame rack, containing four similar slabs. A forklift equipped with a boom attachment and a suspended slab gripper was required for this operation.
The worker and a company director were involved in the process. Initially, they positioned the slab gripper to lift the granite slab with the forklift. Wooden 2x4s were used to create a gap between the desired slab and the one beneath it. As the worker attempted to secure the slab gripper onto the stone slab, the granite unexpectedly tipped forward, falling on the worker.
The incident directly violated Section 45(c) of Ontario Regulation 851, which stipulates that materials, articles, or things to be removed from a storage area, pile, or rack must be handled in a manner that does not endanger the safety of any worker. Furthermore, the company failed as an employer to ensure that these safety measures and procedures were followed in the workplace, contravening section 25(1)(c) of the Occupational Health and Safety Act.
The court's decision serves as a stark reminder to health and safety professionals about the vital importance of robust safety protocols and training programs within workplaces that involve the handling of heavy materials. Ensuring the proper removal of materials from storage areas, piles, or racks is not only a legal requirement but a moral obligation to protect the well-being of workers.
The closure of GTA Granite and Marble Countertops Inc. serves as a somber testament to the consequences of negligence in workplace safety.
Source: The Safety Mag Nov 23
Digital Training Aids & Slide Presentations
Digital Training Aids are designed specifically to complement our Operator Reference Manuals and are available in downloadable or internet versions.
These graphic training aids are a stunning slide show collection of the most accurate and colorful imagery on the market today.
Forklift Operator Training Slide Presentations are an invaluable training aid for your forklift operator certification programs.
Each presentation is designed to provide visual stimulation while reviewing the Operator Reference Manual.
Ask Bob
Hi Bob,
Question:
Hi, can you please advise on the training procedures and requirements for providing training for a forklift attachment, specifically the work platform.
Would I just provide regular forklift training but using the attachment and following instructions from the manufacturer and CSA Standards?
Answer:
Yes, you are correct in that you will need to familiarize yourself with the attachment that will be used with the forklift and follow all applicable regulations and standards for the installation and use of the attachment, as well as the manufacturer’s operation/user manuals.
Section 13.30 in WorkSafeBC OHS regulations addresses forklift mounted work platforms so you definitely want to check that out. Also, CSA B335.15 references it in Section 4.9.9 of that standard.
I, personally, am not a fan of work platforms being used on forklifts because of so many issues that could occur such as; ‘not ANSI approved’, ‘not properly mounted’, ‘not approved by the manufacturer’, ‘not properly trained’, etc.
I recommend using a scissor lift or another type of elevating work platform that is actually made for the job of lifting people into the air over a forklift with a platform.
Bob
Interesting Articles
- Competitive forklift is the new motorsport?...more.
- Top 10 forklift safety tips every worker should know...more.
- Construction worker killed in excavator collapse in Delray Beach [VIDEO]...more.
- Worker crushed after hay bales fall from front-end loader...more.
- Thieves use backhoe to break into store with clerk inside [VIDEO]...more.
- Man steals excavator to build himself a home in public Seattle Park…more.
- Employee dies after being trapped beneath forklift ...more.
- Firefighters rescue two men from boom lift...more.
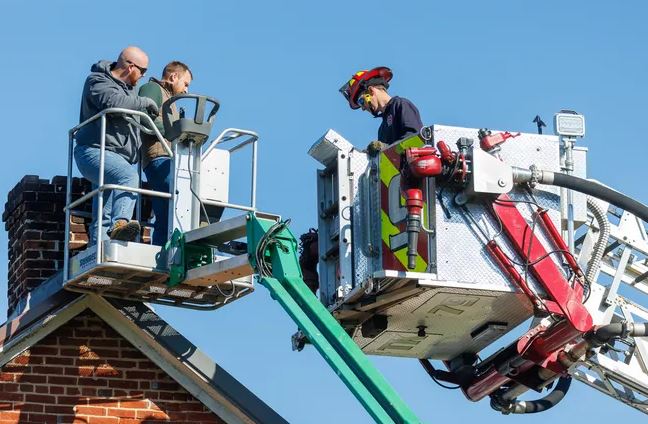
Client Testimonials
"Training material is very easy to follow. Step by step layout makes it easy to keep training sessions similar so no steps are missed."
Jason, Premium Combo Train the Trainer.
"This is probably the most relevant training I have received in all my years at this company. It was very engaging and informational."
Joel, Custom MEWP Train the Trainer Program.
"I truly feel empowered by the information received."
David, Premium Combo Train the Trainer Program.
Did you enjoy this newsletter? Sign up for our newsletter to receive more like this!