But first, check out all the places we are delivering training this month...
B. Class 2 – Order Picker
C. Class 1 – Counterbalanced Rider Types, Stand-up
You can also look forward to seeing a Spanish language version of the new NA ORM as well as revised operator requalification materials very soon!
Regardless of industry sector, almost every business will have seasonal peaks to manage. Whether it be promotions such as Black Friday, pre-Christmas preparations or other sector-specific pressures, such upticks in demand often rely on recruitment to supplement the workforce and boost efficiency.
When taking on a new starter during a busy period, employers can be keen for a new recruit to start working productively, as soon as possible. But without ensuring that the newest member of your team is ready to start work safely, you will be putting them, those around them and your business at risk.
Indeed, research shows that workers are four times as likely to be involved in an accident during the first month of their employment than at any other time, so it’s vital that they are fully prepared before joining the ranks of your workforce.
Employers have a duty of care to all new starters, from day one. Let’s take a look at four key steps you can take to help them stay safe:
1. Verify experience and qualifications
When it comes to lift truck operators, in the UK, there’s no such thing as a forklift licence.
Any operator undergoing formal training should receive a certificate demonstrating that they have successfully completed basic training on the specified category of truck, so be sure to check their certification or proof of operation.
We strongly recommend that training is accredited by one of the accrediting bodies that form the Accredited Bodies Association for assurance of the standard of training delivered.
Take the time to check how recently the training took place and verify the details with the relevant accrediting body or training provider.
The next stage is to assess current operational skills. This will help to gauge the present standard of the operator and determine what training is required before they can safely begin using forklift trucks on your site. This can be carried out by an external provider or in-house by a qualified, competent person.
2. Provide proper training
In the UK, operators must receive three essential elements of forklift training before being allowed access to MHE (basic, job specific and familiarisation).
However, training should not be limited to forklift operators alone. New colleagues working around forklift trucks are at serious risk of injury if they are not made aware of the risks and how to navigate their new working environment safely.
Safety awareness training for anyone required to work in the vicinity of forklift trucks will ensure they understand how to help keep themselves and others safe and is therefore a good investment.
And remember, training requirements for new starters apply to everyone, regardless of contract type. Just because a worker may not be a permanent member of your team, your duty of care still applies during the time they are with you, so there’s no justification for training them any less thoroughly than your full-time, employed staff.
In the UK, the Approved Code of Practice for Rider-Operated Lift Trucks (L117) emphasises that special risk management is required when it comes to temporary workers.
So, any company that considers the time and cost of training for temporary and agency workers as wasteful or even optional, must think again.
3. Keep written records of authorisation
Once all relevant training has been completed, employers must give forklift operators written authorisation before they can use a truck. With a real risk of serious injury (or worse) resulting from forklift accidents, there’s no good argument for putting an unqualified person in control.
To prevent unauthorised access to your trucks, ensure there is a robust, communicated system when it comes to handing out keys, or consider more tech-based solutions such as PIN keypads or programmable fobs.
These not only make it far more difficult for unauthorised people to use a truck, but it also encourages individual employees to take greater responsibility for their own access credentials.
4. Regular monitoring and supervision
As well as providing training, its vital that businesses offer new starters sufficient supervision to ensure they are working safely alongside their colleagues.
Like any other employee, they should also receive consistent monitoring to ensure best practice learned in training is followed day to day and complacency or bad habits do not set in.
Having a physical presence and "walking the floor" is key, allowing managers and supervisors not only to see operating standards first-hand but also enabling key documentation, such as pre-shift inspection records to be checked.
However, other methods such as CCTV and truck telematics can also be useful tools to help identify and curb dangerous behaviour.
Whether a new starter is with you for a day or a lifetime, your investment in them will be minimal compared to the returns it can offer, including:
- Improved productivity and less downtime – studies show that safe workers are more productive workers. Fewer accidents mean less time is lost due to clean up, aisle shutdown, or out of action equipment/personnel.
- Lower damage/repair costs – skilled operators protect your bottom line as less is spent on lost stock, truck and racking repairs, new pallets, etc.
- Legal compliance – providing sufficient training will help you meet your requirements and avoid the hefty fines, court costs, and compensation associated with accidents.
- Safer staff – most important of all, you will be protecting your workforce and making sure everyone gets home safe.
Source: Forkliftaction News Aug 2023
Casting Call: IVES Certified Trainers
Would you be interested in appearing in future IVES training videos? Do you live near one of our Open Enrollment training sites?
- Abbottsford, BC
- Prince George, BC
- Oshawa, ON
- Sacramento, CA
- Rancho Cucamonga, CA
- Kapolei, HI
- Bismarck, ND
- Chester, VA
- Irving, TX
- Salt Lake City, UT
- Omaha, NE
We are in the process of planning new video content and plan to shoot much of the footage while our upcoming train-the-trainer programs are taking place.
We would be working around the class, utilizing the classroom and equipment while they are not in use.
Willing participants should be prepared to play the roles of both trainer and operator for various scenarios.
Look at our upcoming schedule and send an email to info@ivestraining.com if you would like to be involved in any future projects.
Tell us your name, the location you could get to, once we have enough participants at any location for a period of 2-5 days, we’ll set some dates and let you know when a filming session is confirmed.
Thank you to everyone for your consideration.
The IVES Team
Incident Report: OSHA fines company $300k USD after forklift fatality.
Federal investigators found a wire manufacturer could have prevented an employee’s death by following workplace safety standards, and issued two willful citations and proposed almost $300,000 in penalties.
Classified by the U.S. Department of Labor’s Occupational Safety and Health Administration (OSHA) as “serious” violations, the sanctions stem from the death of a worker at the company’s San Antonio facility in February.
WMC San Antonio LLC, now based in The Woodlands, allowed the employee to ride on top of an “unsecured, site-made forklift attachment” that was moving wire mesh bundles to a flatbed trailer. The attachment slid off the forks and the employee fell, suffering fatal injuries.
The company had tasked workers with moving material from the plant to another WMC location as the company prepared to close the San Antonio facility, according to a news release from OSHA.
“WMC San Antonio ignored the well-documented dangers of using unauthorized forklift attachments and an employee’s family, friends and co-workers are left to grieve their loss,” stated Alex Porter, who serves as OSHA’s area director in San Antonio. “This company publicly claims that employee safety and well-being is a priority but then unnecessarily exposed workers to serious dangers.”
After opening an investigation into the death, OSHA issued WMC one willful citation for “failing to provide fall protection for employees working at heights up to 13 feet” and a second for “exposing workers to fall and struck-by hazards by allowing them to ride on improper and unsecured forklift attachments.”
The agency has proposed $299,339 in penalties for its violations. According to the notification letter to WMC, the company has a total of eight violations it must correct. It must act within 15 days to contact OSHA and either pay the fine and correct the violations or contest them. A call to WMC was not immediately returned Monday afternoon.
According to its website, WMC is a “family-owned company” that offers “custom steel wire solutions” and “values the safety and well-being of all team members as our number one priority.”
WMC is part of the Turia Group, according to the website, which “leads and innovates the steel industry with a global vision.”
The U.S. Department of Labor release described WMC, which appears to stand for Wire Mesh Company, as being founded in 2003 in Jacksonville, Florida, with mill facilities in Texas, California, Illinois, Pennsylvania and South Carolina. The company lists a West Commerce Street address on its website.
Source: San Antonio Report Aug 2023
Interesting Articles
- Scissor Lift accident results in four deaths...more.
- Police investigating forklift death...more.
- Company fined after warehouse worker struck by reversing forklift…more.
- Worker pinned under front-end loader critically injured...more.
- Water gushing out of pipeline lifts 21-tonne Excavator [VIDEO]...more.
- Forklift driver dies after airport accident...more.
- Man charged after taking a scissor lift for a joyride [VIDEO]...more.
- Injured bear climbs tree and gets rescued by Boom Lift...more.
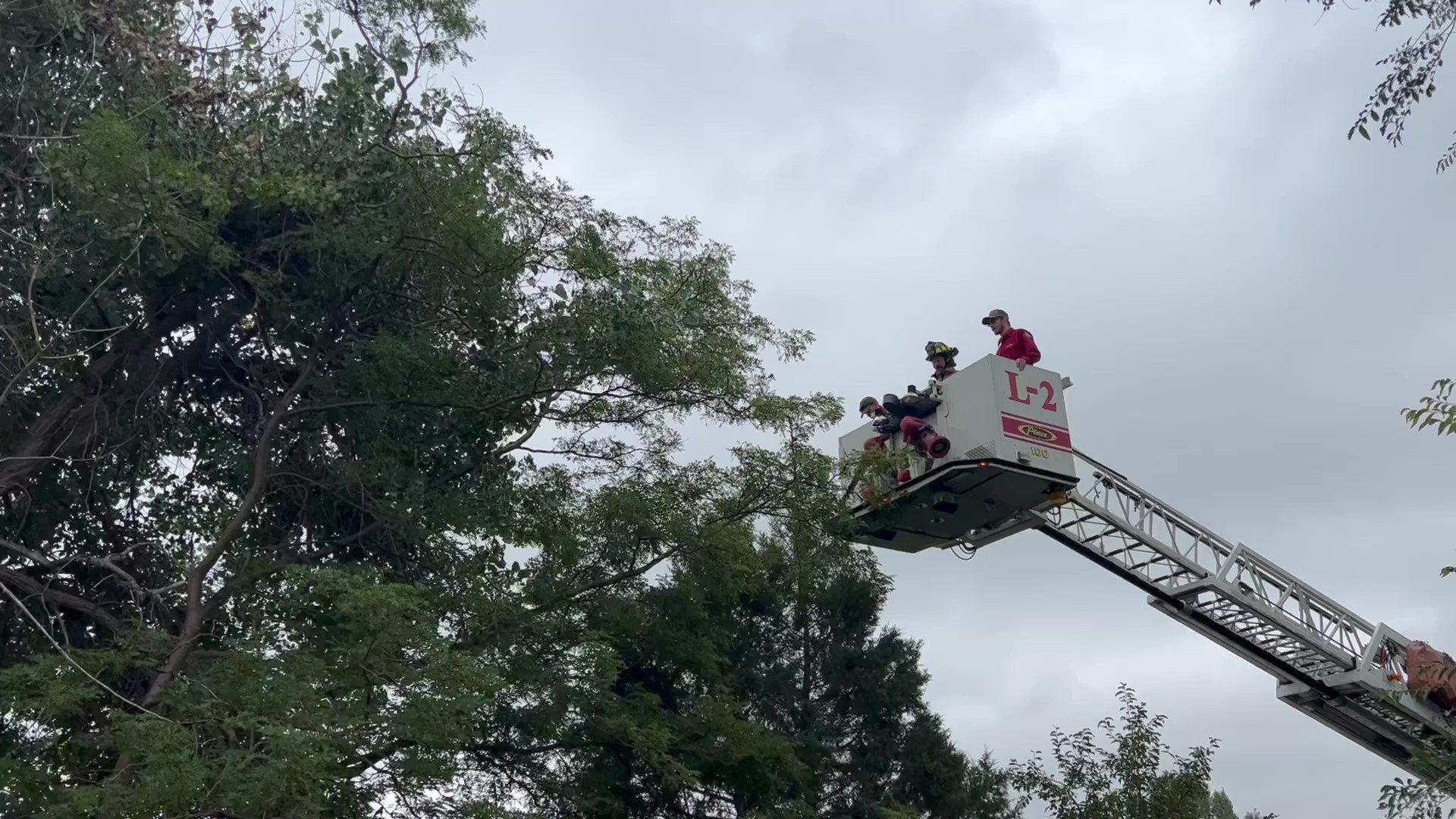
Client Testimonials
“Third trainer class I have had done onsite, third different instructor, and continue to be amazed! This program, the people from admin to trainers, are by far the best in every way. Will continue to use and always highly recommend!”
Daniel, Custom Train the Trainer Program.
“I really enjoy the flexibility and ease of these remote training options. This is the third time I have gone through for the renewals and it has been easier and more streamlined each time.”
Jose, Online Trainer Recertification Program.
Did you enjoy this newsletter? Sign up for our newsletter to receive more like this!