Ignoring or engaging in risky behavior might be a perception issue
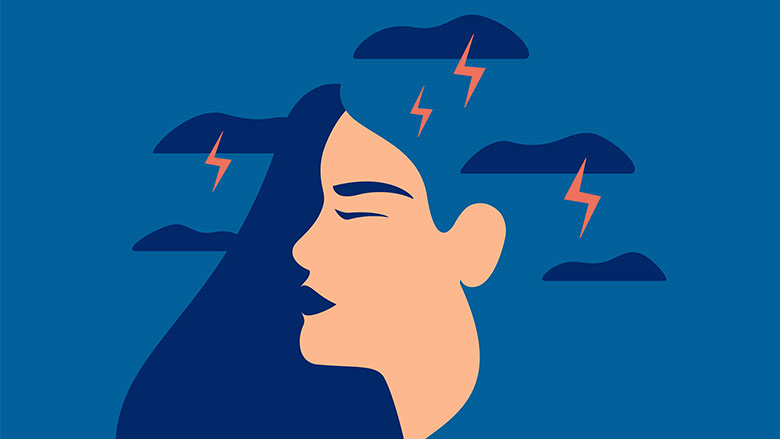
It is a researched fact that a person’s perception of risk or their tolerance of it, will in one way or another influence their decision-making and impact their safety.
Awareness of this fact is a prerequisite for effectively managing risk and designing preventive measures.
If at work you hear statements similar to the ones indicated below or after an accident:
- I have done this a hundred times before with no problems what so ever.
- I do riskier things than this in sports and at home.
- It’s not that bad, we all have done so before.
- It will only take a minute, it’s no big deal.
- But we told them, trained them, posted signs, and yet they do stupid things like this.
Why would any experienced or sane person do that?
Risk tolerance has been defined as a desire, motivation, or willingness of a person or a group to engage in behaviors that exposes them to the potential of getting injured.
The factors that influence people to accept risk varies with individuals, may be impacted by group dynamics, possibly affected by management, the work climate as well as the organizational culture.
Understanding and addressing this will influence the management of the safety outcomes on the worksite.
Risk perception involves the ability of workers to look at their work environment and identify hazards, then perceive the associated risk, understand how the hazard could result in an incident or harm as well as assess the degree of its severity.
This ability is dependent on their past experience, knowledge and their ability to predict the potential consequences of being exposed to the condition.
Those that have deficiencies in this regard may require additional through a review of relevant incidents training, or coaching which show how situations have or could have resulted in an incident, injury or loss.
Generally, most organizations have some traditional safety practices such as inspections to find unsafe conditions and correct them, as well as training, or feedback to workers during site inspections to minimize unsafe behaviors on the workers’ part. In all likelihood this is the primary work performed by the safety manager or practitioner in trying to control the company’s accident and the injury rate.
The safety manger may also have other responsibilities in regard to the management of safety as well. These practices and/or interventions do not really effectively address an individual’s risk-tolerance or propensity to engage in at risk behavior.
Recognition of hazards and acceptance of risk
Basically, the risk of injury can exist in the work environment, the organizational as well as operational systems, or result from some action on the worker’s part.
There are five means or methods that are at play in creating or recognizing situation where a hazard may be created or exist which may potentially cause an accident, injury or loss.
These involve risk recognition, assessment, acceptance as well as the means to eliminate it or reduce their adverse effect.
Sources of physical hazards or risk
In all likelihood on a construction worksite just about every physical hazard or risk of injury encountered by the workforce may have been created by the action of workers putting work in place at some earlier point in time.
Other risks may be created by supervision or management while planning, organizing, directing, assigning, or controlling the work.
Risk may also come from the design, interaction, or influence of operational and organizational systems, the organizational culture, the work climate as well as management and supervisions, actions, behaviors or expectations, as utilized, understood or perceive by the worker.
And finally, the project design may contain inherent risks, The following 4 points
Risk-tolerance generally occurs over time.
Workers may take shortcuts when performing their work for any number of reasons and encounter no negative outcomes.
This will eventually desensitize them to those risks and cause them to accept the at-risk behavior as the way they routinely preform all their work going forward.
This paper will primarily deal with the decision and action taken by the individual worker as listed in items 3 through 5 above.
Potential risk-tolerance interventions
One way to deal with the workforce’s acceptance of greater risk than what is deemed reasonable or acceptable by the organization, as well as minimizing their adverse effect is to anticipate such potential outcomes.
The best way to address this is to engage in a robust and systematic preplanning effort of all tasks and/or activities before their start and error-proof them as much as possible so as to reduce the risks faced by their workforce when they are assigned to those tasks. (Look for a paper on effective preplanning coming in the near future).
Item 1 above will be dealt with in multiple papers in the future.
The way to determine if an individual worker tends to accept more risk than is deemed acceptable is to observe them if they are new to the worksite or every time, they are assigned a different kind of task from the one they have been performing.
The workers who are identified as risk takers are dealt with as follows:
Experience factors
Familiarity with the work may cause the worker’s attention to wonder and as a result become unaware of any potential hazard that may develop during work, or wonder into what is known as ‘the line of fire’ which will in all likelihood result in an incident with negative consequences.
Having performed similar work over a long period of time may cause the worker to become over confident in their ability and as a result underestimate the severity of the risk and thereby fail to take ample precautions potentially leading to an incident with serious consequences.
Perception factors
Over confidence in one’s capabilities, knowledge, or experience may result from past experience in having performed similar tasks in a certain way successfully even though the method involved a level of at-risk behavior.
At a subsequent instance there may be a small difference with the level of risk or conditions may change, but overconfidence in the worker’s ability may over shadowed this which may lead to a negative outcome.
The level of risk may be perceived as acceptable, when in reality the worker under estimates it.
Therefore, the worker proceeds with the work without changing the means or methods which could lead to an accident.
The associated risk of the task is determined to have a minor or insignificant negative outcome.
So, the worker proceeds with the work but unfortunately is involved in an accident whose consequences result in a serious injury.
Difficulties with safety factors
Completing daily task assignment may cause the worker to choose to rush because he realizes that this will not be possible given the remaining time left in the work day.
So, rushing to meet he goal, may cause the worker to engage in at-risk behavior which may result in an incident with a negative outcome.
The personal protective equipment is uncomfortable or hinders production.
This could involve safety glasses that fog up requiring multiple stoppages to clean away the moisture, as well as others.
In order to meet the production goal set by the superintendent the worker chooses to remove the safety glasses or other PPE and continue without them.
This increases the risk of a potential eye injury, or another loss.
The workforce needs to receive appropriate training which enables them to identify the existence of the risk of injury in the work environment.
After having made the identification, they may need to be coached in order to enable them to make a determination of the level or seriousness of the risk.
The next step for the worker, is to make and evaluate the level of the risk as compared to the organizational acceptable standard, in order to safely proceed with the work.
Supervision must be cognizant that this is where the worker’s risk-tolerance may come into play and possibly override caution.
The worker’s risk-tolerance can be brought in line with the organizational predetermined level through proper training followed by careful oversight as well as coaching and feedback,
This, will eventually align the worker’s risk tolerance level in line with that of the organization.
To reinforce this, the organization must make it “safe” for the worker to inform supervision that they will not proceed with the work if they determine that the existing level of risk is too high and that certain changes need to be made in order to safely proceed with the work.
The diligent management of the reinforcement process will invariably make the workers risk-tolerance come into line with organizational expectation.
Conclusion
Research has shown that different people are likely to see hazards and their associated risks as well as how to address them in different, sometimes contradictory ways.
Incomplete and differing knowledge leaves considerable room for different plausible choices or approaches to dealing with encountered situations or conditions.
Judgments about the same evidence can vary, and both judgments and the underlying analyses can be influenced by the situational reality, individual experience, as well as values held by each individual.
It is important for project supervision supported by the safety manager to provide the appropriate training, provide on-the-job support, coaching and feedback.
Management must create a work environment which enables the worker to seek guidance, discuss concerns and receive support in improving their risk identification, assessment and determination of the appropriate level of the existing risk.
Product Feature: Wallet Card Template
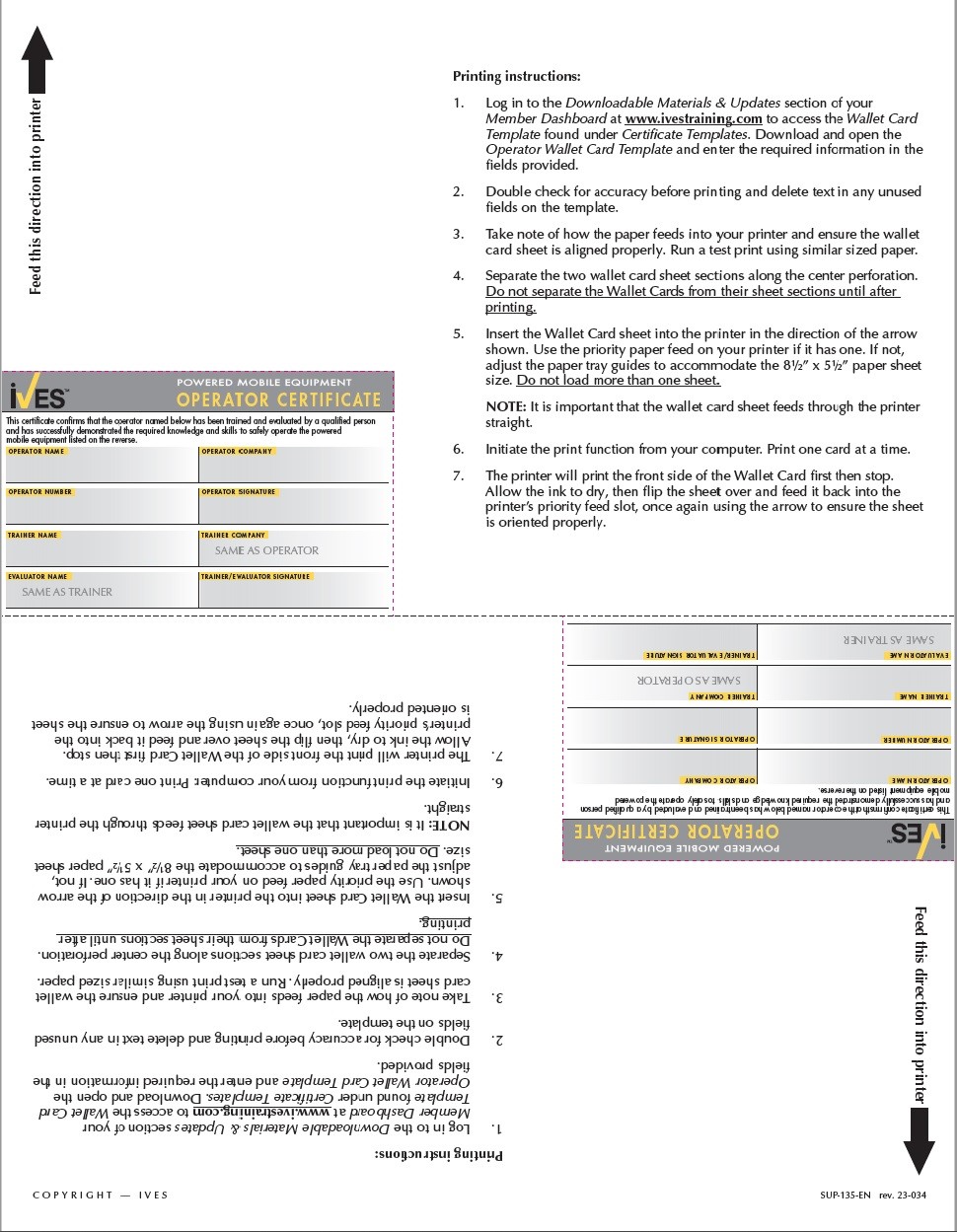
You Spoke and We Listened: New Wallet Card Printer Template
In response to requests we’ve received from Trainers like you to improve the printing process for the Operator Wallet Cards included our Requalification Notepads, we are very happy to announce that we have done just that.
Previously, eight Wallet Cards were provided at the back of the Notepads on a thick sheet of card stock that was difficult for most printers to handle smoothly, which often led to Wallet Cards being ruined. The problem was compound by the need to use a process and template that were less than ideal.
We have solved these issues by first, placing the Wallet Cards in the Notepads on four separate sheets made of slightly thinner stock, with two cards on each sheet. Second, by developing a new printer template and process that is far easier to use. Testing showed these improvements to be very effective in eliminating the previous issues and produced printed Wallet Cards that were neat, sharp and clean.
The new Operator Wallet Card printer template, complete with detailed instructions on its use, along with a brief tutorial video are available in the "Downloadable Materials & Updates, Certificate Templates" area of your Member Dashboard at
https://www.ivestraining.com/SignIn.
The updated template is available for IVES Certified Trainers now. Some Operator Requalification Notepads, including the new sheets with 2 wallet cards on them, are shipping in orders now and we expect all of them to be revised and in circulation before the end of the year.
We hope you appreciate these improvements as much as we appreciate you providing the incentive to make them.
The IVES Training Team
Incident Report: Kitchen Installer fined $33K USD over forklift incident.
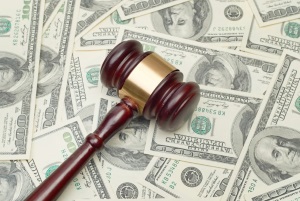
Trendgosa Pty Ltd, was sentenced in the Heidelberg Magistrates’ Court last Wednesday after pleading guilty to a charge of failing to provide or maintain systems of work that were, so far as reasonably practicable, safe and without risks to health.
The company was ordered to pay $2,698 in costs.
In December 2021 a forklift driver was unloading a shipping container at the company’s Heidelberg West warehouse.
As the forklift exited the container carrying a loaded pallet, the load fell from the forklift’s forks and struck a worker standing outside.
The injured worker suffered fractures to his skull, temple, shoulder blade, collar bone and ribs, and punctured lungs.
A WorkSafe investigation found the forklift driver did not have a current High Risk Work Licence for forklift operation and that the company did not have a traffic management plan to protect pedestrians when unloading shipping containers.
The court heard it was reasonably practicable for the company to have a traffic management plan and set up a three-metre exclusion zone, such as by using bollards and barricade tape, to prevent anyone entering the area while the forklift was operating.
It was also reasonably practicable to ensure that the forklift was stopped and that any loads were positioned to prevent them coming into contact with anyone, prior to the forklift operator permitting anyone to enter the exclusion zone.
WorkSafe Director of Health and Safety Narelle Beer said this was a serious breach and that too many employers still failed to control the well-known risks associated with forklifts.
“Working with forklifts is inherently hazardous and employers must be proactive to protect workers and others from the risk of being struck by a load or a moving forklift,” Dr Beer said.
“That means using a traffic management plan, including measures to separate pedestrians from moving vehicles and loads, such as barriers, exclusion zones and warning signs.”
Since January 2022, fines totalling $775,000 were imposed by the courts against companies and directors in 13 WorkSafe prosecutions involving forklifts. In the same period, WorkSafe has accepted 192 claims from workers seriously injured in forklift incidents and since February 2019, eight people have died as a result of forklift incidents.
Employers using mobile plant such as forklifts should ensure:
- A traffic management plan is in place for pedestrians and powered mobile plant and that it is reviewed and updated as appropriate.
- Pedestrians are separated from moving machinery and that an effective communication system between operators, transport contractors and ground staff is in place.
- Signage is in place and barriers are erected where appropriate.
- Visibility issues are identified and controlled, particularly if lighting is poor.
- Workers operating equipment have the appropriate high risk work licences, as required.
- Machinery and vehicles and regularly inspected and maintained by a suitably qualified person.
- Employees and health and safety representatives are consulted about health and safety issues.
Ask Bob
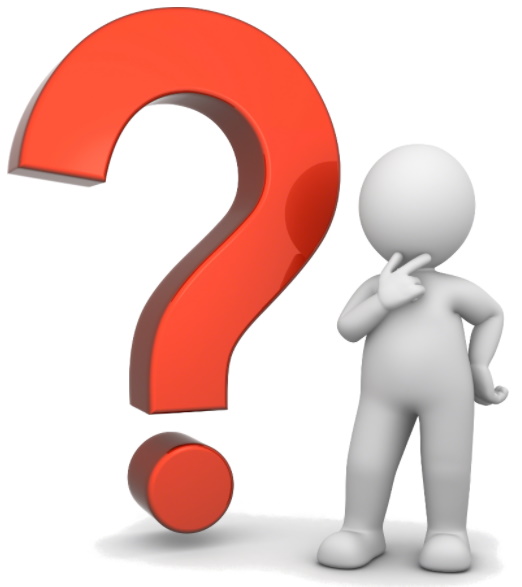
Free technical support for all IVES Certified Trainers!
Question:
Hi Bob,
When creating a MEWP program, should it include a signal person?
I am being told my program does not include a signal person for being near power lines, however I address the power line hazard and distances in the program.
I don't recall covering signal person in the course I took.
Answer:
Thanks for checking in with us.
Teaching hand signals can be a part of an operator training program if a signal person/spotter is need or used.
There are no mandatory requirements for a signal person but company policy may exceed the requirements of regulations/standards with a company rule that necessitates the use of a signal person within certain specified distances of power conducters.
At that point, it would be beneficial to train spotters to use the hand signals developed by your company or others used in general industry.
In either case, the main concern is that the operator and spotter are of the same understanding on the use and meaning of the signals used.
Bob
Interesting Articles
- Forklift topples on factory worker, killing him...more.
- Prince Harry and Prince Louis operate an excavator [VIDEO]...more.
- How does OHSA define an accident...more.
- Several men escaped serious injury after boom lifts collapse [VIDEO]...more.
- Trucking company fined after mechanic dies while repairing forklift...more.
- Suspect arrested after stolen forklift is taken on a wild ride [VIDEO]...more.
- What to remember when operating a forklift...more.
- Telehandler falls into canal...more.

Client Testimonials
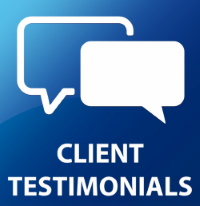
"Having a good, knowledgeable instructor makes a huge difference. I would recommend this training program." Ryan, Express Forklift Program.
"I learned a tremendous amount each day, both classroom and practical. My time and company’s money were well spent." David, Premium Combo Train the Trainer Program.
"Liked everything about the program. Learned a tremendous amount. Really liked the material covered and the knowledge of the trainer." Dennis, Custom Trainer Program.